含硫含碱废液过程减排新技术及在化工行业中应用
项目名称:含硫含碱废液过程减排新技术及在化工行业中应用
奖励类别:国家科技进步奖
获奖等级:二等
授予单位:中华人民共和国国务院
获奖单位:华东理工大学,中国石化集团资产经营管理有限公司巴陵石化分公司,中国石油化工股份公司镇海炼化分公司,中国石油天然气股份有限公司克拉玛依石化分公司
项目完成人:汪华林,黎树根,钱卓群,胡江青,白志山,杜海波,张明会,刘成军,唐新华,瞿滨
获奖时间:2009
成果介绍:
该项目属循环经济与节能减排技术领域,涉及石油化工清洁生产工艺、化工过程机械和环境保护机械设备设计与制造技术。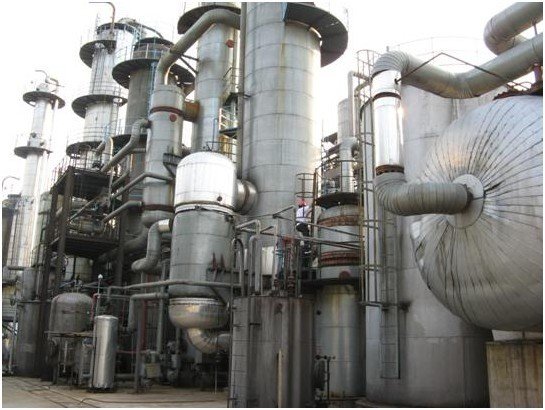
我国石油脱硫与后续转化过程中每年消耗碱性原料2万吨,产生含硫含碱废液(水)约4500万吨,涉及面广,有重大安全风险。国外加氢脱硫和转化回收技术,既治理污染,又回收资源。我国也采用同类技术,但原料消耗多、废碱回收率低、能耗高、排放COD高。
项目组从含硫含碱废液"减量、全回收、无污染"的"过程减排"出发,在三锥体旋流器的基础上研制了低能耗单锥体微旋流器,使能耗从0.2MPa降低到0.1MPa。引入聚结剂,形成全新的微量纳尺度杂质聚结旋流捕集技术与装置,使混合C4中醇胺分子的浓度降低0.04mg/kg,聚结剂中醇胺浓度从1.02mg/L增加到24.03mg/L;使环己烷氧化液的钠离子浓度从旋流脱碱器出口10.76mg/L再降低到2.52mg/L,使液-液分离精度从旋流脱碱的微米级延伸到聚结微旋流的纳米级,有重大突破,且单锥体微旋流器成为GB/T国家标准。
项目发明了废碱膨化燃烧技术及其熔碱饱和造粒全回收新技术,以膨化剂延缓固形物沉降,降低废碱液焚烧成本;以饱和碱液做媒质,使熔碱雾化-冷却-结晶协同进行,高浓度废碱液的碱回收率由70%提高到约100%,无废水排放,实现"饱和碱液封闭循环,熔碱全回收"。
项目开发成功富氧氧化-重力沉降-旋流-聚结旋流捕集—反应再生新工艺技术,使环己酮生产过程碱消耗量减少30%,产量增加8%;使甲基叔丁基醚生产过程催化剂单耗降低40%,离子保护剂连续运转周期提高4倍;使含硫废液汽提塔蒸汽消耗量从0.22吨/吨废水降低到0.12吨/吨,汽提过程的连续稳定运转周期提高1倍。
该技术申请中国发明专利15件,美国、荷兰发明专利各1件,授权中国发明专利4件,实用新型专利1件,还制定了聚结旋流微相捕集的单锥体微旋流器的GB/T国家标准(已完成报批手续,待正式发布)1项。经专家鉴定,整体技术国内首创,处国际先进水平,部分指标处国际领先水平。
项目建成6种类化工装置的含硫含碱废液过程减排示范工程,应用到18个省市的44套化工生产装置,环己酮占全国总产量的65%,含硫废液汽提处理能力1112万吨/年,干气和液化石油气脱硫处理能力314万吨/年,占全国总量的17.2%,甲基叔丁基醚占全国总量的10%。近三年,原料碱消耗减少7.44万吨,减少COD排放12.5万吨,减少二氧化硫排放1.15万吨,减少蒸汽消耗262.5万吨,减少废热排放2.14×109MJ,回收污油1.3万吨,回收废碱3万吨,新增利税12.1亿元,消除了18个省市含硫含碱废液的44个点源,经济和社会效益重大。
该创新技术实现含硫含碱废液过程减排技术的跨越式发展,推动化工工艺环保科技进步,提高炼油行业应对原油高硫化的竞争力,此外,还可应用到煤气化、聚氯乙烯、乙烯、纯碱、钢渣、天然气及合成气脱硫等生产中。